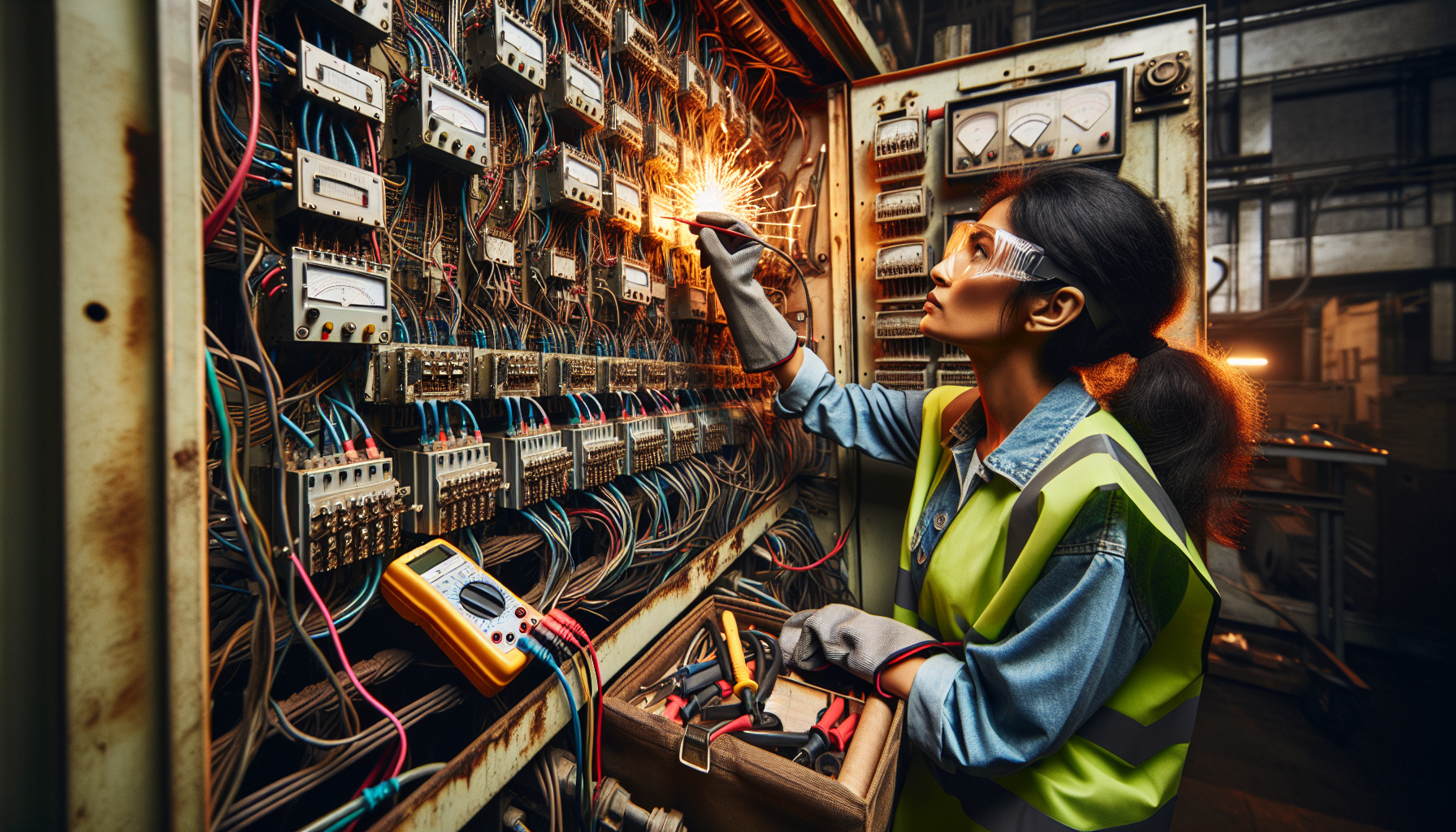
electrical machine breakdown
Minimize Downtime and Maximize Efficiency: Proven Strategies to Reduce Machine Breakdowns
Reducing machine breakdowns is crucial for maintaining smooth operations and productivity. Implementing proactive measures ensures longevity and reliability of equipment while minimizing costly disruptions.
✓Implement Preventive Maintenance: Schedule regular maintenance checks to identify and address potential issues before they lead to breakdowns. Include lubrication, cleaning, and part replacements in the routine.
✓Trained Operators: Ensure that machine operators are well-trained on proper equipment handling, troubleshooting, and recognizing early signs of malfunction.
✓Use Predictive Analytics: Leverage advanced technologies such as loT sensors and data analytics to monitor equipment health in real-time, predicting potential failures and preventing unplanned downtime.
✔Maintain a Spare Parts Inventory: Keep critical spare parts readily available to reduce downtime caused by waiting for replacements. This ensures quick fixes and minimizes the impact on production.
✓Conduct Root Cause Analysis: After any breakdown, perform a detailed root cause analysis to understand and address the underlying issue, preventing recurrence.
✓Standardize Operating Procedures: Develop and enforce standard operating procedures (SOPs) to ensure consistent equipment use and minimize operator errors.
✓Optimize Lubrication Management: Use the right lubricants and apply them correctly to reduce wear and tear on critical components, extending equipment lifespan
.Proactively managing maintenance and using technology to monitor equipment health are key strategies to significantly reduce machine breakdowns and improve overall operational efficiency.
we have detailed explanation for major electrical machines and equipment maintenance in our website ” maintenance category”.