Corrosion Monitoring is a process that evaluates and monitors equipment components, structures, process units, and facilities for signs of corrosion. Monitoring programs aim to identify certain conditions in order to extend the life and serviceability of assets while increasing safety and reducing replacement
costs. Corrosion monitoring covers all types of corrosion and materials. The key advantage to implementing corrosion monitoring is to detect early warning signs of corrosion and to determine trends and processing parameters that may induce a corrosive environment. Processing parameters that may need to be altered include temperature, pressure, pH, etc. Additionally, corrosion monitoring serves to measure the effectiveness of corrosion prevention methods in order to determine if different inspection and/or monitoring techniques should be utilized.
CORROSION MEASUREMENT TECHNIQUES
A wide variety of corrosion measurement techniques exists, including:-
*Ultrasonic testing *Non-Destructive Testing *Radiography * Thermography * Eddy current/magnetic flux * pH measurement *Dissolved gas (O2, CO2, H2S) * Metal ion count (Fe2+, Fe3+) * Microbiological analysis * Operational Data * pH * Flow rate (velocity) * Pressure * Temperature * Fluid Electrochemistry * Potential measurement * Potentiostatic measurements * Potentiodynamic measurements * A.C. impedance *Corrosion Monitoring * Weight loss coupons * Electrical resistance * Linear polarization * Hydrogen penetration * Galvanic current
CORROSION MEASUREMENT TECHNIQUES
- Some corrosion measurement techniques can be used on-line, constantly exposed to the process stream, while others provide off-line measurement, such as that determined in a laboratory analysis. Some techniques give a direct measure of metal loss or corrosion rate, while others are used to infer that a corrosive environment may exist.
- Corrosion monitoring is the practice of measuring the corrosivity of process stream conditions by the use of “probes” which are inserted into the process stream, and which are continuously exposed to the process stream condition. Corrosion monitoring “probes” can be mechanical, electrical, or electrochemical devices.
- Corrosion monitoring techniques alone provide direct and online measurement of
metal loss/ corrosion rate in industrial process systems.
Typically, a corrosion measurement, inspection and maintenance program used in any industrial facility will incorporate the measurement elements provided by the four combinations of on-line/ off-line, direct/indirect measurements. - Corrosion Monitoring Direct, On-line
- Non-Destructive Testing Direct, Off-line
- Analytical Chemistry Indirect, Off-line
- Operational Data Indirect, On-line
In a well-controlled and coordinated program, data from each source will be used to
draw meaningful conclusions about the operational corrosion rates with the process
system and how these are most effectively minimized.
Why is it Important?
Corrosion is a major threat to the oil and gas, petrochemical and other process-intensive industries and is responsible for countless of dollars in damage and maintenance costs. Additionally, ageing equipment becomes more susceptible to corrosion and loses its ability to withstand harsh operating environments (e.g. high temperature and pressure). The purpose of a strong corrosion monitoring program is to improve safety, reduce maintenance and inspection costs, and maximize efficiency.
The rate of corrosion dictates how long any process equipment can be usefully and safely operated. The measurement of corrosion and the action to remedy high corrosion rates permits the most cost-effective plant operation to be achieved while reducing the life-cycle costs associated with the operation.
Corrosion monitoring techniques can help in several ways:-
1) by providing an early warning that damaging process conditions exist which may result in a corrosion-induced failure.
2) by studying the correlation of changes in process parameters and their effect on system corrosivity.
3) by diagnosing a particular corrosion problem, identifying its cause and the rate controlling parameters, such as pressure, temperature, pH, flow rate, etc.
4) by evaluating the effectiveness of a corrosion control/prevention technique such as chemical inhibition and the determination of optimal applications.
5) by providing management information relating to the maintenance requirements and ongoing condition of plant.
How is Corrosion Monitoring Performed?
Corrosion monitoring covers a broad range of techniques that involve measuring, controlling, and mitigating corrosion. These techniques can be broadly classified into two types:- inspection and monitoring. These corrosion monitoring techniques have been successfully applied and are used in an increasing range of applications because: - The techniques are easy to understand and implement.
- Equipment reliability has been demonstrated in the field environment over many years of operational application.
- Results are easy to interpret.
- Measuring equipment can be made intrinsically safe for hazardous area operation.
- Users have experienced significant economic benefit through reduced plant down time and plant life extension.
Inspection Techniques
Before inspection techniques are applied, it’s important to document the operating parameters of equipment that may be increasing the likelihood of corrosion development. These parameters include, but are not limited to, pH, flow rate (velocity), pressure, and temperature of the system.
Next, nondestructive testing (NDT) and inspection techniques are performed to locate and identify the type of corrosion damage.
*Common NDT methods used to detect corrosion include ultrasonic testing, radiographic testing, and magnetic flux leakage.
*Risk-based inspection and fitness-for-service assessments are additional methodologies and processes that can complement a monitoring program. These methods involve qualitative and quantitative approaches and provide information about the current state of equipment and provide information about the remaining life of equipment. - Once corrosion is identified, corrosion measurement techniques may be used to gather information about the corrosive environment. This is accomplished by the use of probes, which can be mechanical, electrical, or electrochemical devices that monitor changes in corrosivity during operation. Furthermore, corrosion measurement techniques can be used to provide direct and indirect information about a process while on-stream (i.e. during operation) or off-stream. Common corrosion measurements include pH measurements and microbiological analysis. Analytical chemistry techniques can provide information about the amount of dissolved gas (e.g., O2, CO2, and H2S) and the oxidation of metal ions (e.g., Fe2+, Fe3+).
- Corrosion monitoring techniques provide direct measurements while the process unit is operating. Common monitoring techniques include the use of corrosion coupons, electrical resistance, linear polarization resistance, and galvanic monitoring. Advanced monitoring techniques include biological monitoring, ultrasonic thickness monitoring, and hydrogen penetration monitoring.
- Corrosion coupon (Weight/ Mass loss coupon) testing is the simplest form of corrosion
monitoring that can be applied to all environments (e.g. gases, fluids, and slurries). A coupon is
a sample piece that matches the material of equipment to be monitored. The coupons is placed
into a process environment and removed after a period of time (e.g. weeks or months). It is
then analyzed for:
1) the amount of mass lost,
2) the type of corrosion,
3) the rate of corrosion.
The Weight Loss technique is the best known and simplest of all corrosion monitoring
techniques. The method involves exposing a specimen of material (the coupon) to a process
environment for a given duration, then removing the specimen for analysis. The basic
measurement which is determined from corrosion coupons is weight loss; the weight loss
taking place over the period of exposure being expressed as corrosion rate. The simplicity of
the measurement offered by the corrosion coupon is such that the coupon technique forms the
baseline method of measurement in many corrosion monitoring programs.
Corrosion Monitoring Techniques
(i)Corrosion Coupon
The technique is extremely versatile, since weight loss coupons can be fabricated from any commercially available alloy. Also, using appropriate geometric designs, a wide variety of corrosion phenomena may be studied which includes, but is not limited to:- - Stress-assisted corrosion
- Bimetallic (galvanic) attack
- Differential aeration
- Heat-affected zones
In a typical monitoring program, coupons are exposed for a 90-day duration before being removed for a laboratory analysis. This gives basic corrosion rate measurements at a frequency of four times per year. The weight loss resulting from any single coupon exposure yields the “average” value of corrosion occurring during that exposure. The disadvantage of the coupon technique is that, if a corrosion upset occurs during the period of exposure, the coupon alone will not be able to identify the time of occurrence of the upset and depending upon the peak value of the upset and its duration, may not even register a statistically significant increased weight loss. Therefore, coupon monitoring is most useful in environments where corrosion rates do not significantly change over long time periods.
(ii)Electrical resistance (ER)
ER probes can be thought of as “electronic” corrosion coupons. Like coupons, ER probes provide a basic measurement of metal loss, but unlike coupons, the value of metal loss can be measured at any time, as frequently as required, while the probe is in-situ and permanently exposed to the process stream. These probes are able to perform in all environments for long periods of time. Furthermore, they are able to provide periodic (e.g. daily, weekly, monthly) or continuous (e.g. hourly) data about the rate of corrosion.
The ER technique measures the change in Ohmic resistance of a corroding metal element exposed to the process stream. The action of corrosion on the surface of the element produces a decrease in its cross-sectional area with a corresponding increase in its electrical resistance. The increase in resistance can be related directly to metal loss and the metal loss as a function of time is by definition the corrosion rate. Although still a time averaged technique, the response time for ER monitoring is far shorter than that for weight loss coupons. The graph shows typical response times.
ER probes have all the advantages of coupons, plus:- Direct corrosion rates can be obtained.
- Probe remains installed in-line until operational life has been exhausted.
- They respond quickly to corrosion upsets and can be used to trigger an alarm.
ER probes are available in a variety of element geometries, metallurgies and sensitivities and can be
configured for flush mounting such that pigging operations can take place without the necessity to remove probes. The range of sensitivities allows the operator to select the most dynamic response consistent with process requirements.
(iii) Linear Polarization Resistance (LPR)
The LPR technique is based on complex electro-chemical theory. For purposes of industrial measurement applications, it is simplified to a very basic concept. In fundamental terms, a small voltage (or polarization potential) is applied to an electrode in solution. The current needed to maintain a specific voltage shift (typically 10 mV) is directly related to the corrosion on the surface of the electrode in the solution. By measuring the current, a corrosion rate can be derived. The
advantage of the LPR technique is that the measurement of corrosion rate is made instantaneously. This is a more powerful tool than either coupons or ER where the fundamental measurement is metal loss and where some period of exposure is required to determine corrosion rate. The disadvantage to the LPR technique is that it can only be successfully performed in relatively clean aqueous electrolytic
environments. LPR will not work in gases or water/oil emulsions where fouling of the electrodes will prevent measurements being made. The major disadvantage to this technique is that it can only be performed in conductive media and in aqueous solution.
(iv) Galvanic monitoring, also called zero resistance ammetry, is another electrochemical technique that measures galvanic current passing between two dissimilar electrodes. The results provide information about the oxygen content in the media. Biological monitoring measures the presence of bacteria that consume sulphate and generate sulphuric acid (H2SO4). Biological monitoring and analysis generally seeks to identify the presence of Sulphate Reducing Bacteria – SRB’s. This is a class of anaerobic bacteria which consume sulphate from the process stream and generate sulphuric acid, a corrosive which attacks production plant materials. Ultrasonic thickness monitoring is a very common NDT method that measures the wall thickness of a component over time. This technique is extremely sensitive and is capable of scanning over large surface areas using ultrasonic waves.
(v) Hydrogen penetration monitoring uses probes to measure the amount of hydrogen that dissolves into steel components. In the oil and gas industry, hydrogen is often a by-product in many reactions and can lead to hydrogen induced cracking or hydrogen embrittlement if left untreated. In acidic process environments, hydrogen is a by-product of the corrosion reaction. Hydrogen generated in such a reaction can be absorbed by steel particularly when traces of sulphide or cyanide are present. This may lead to hydrogen induced failure by one or more of several mechanisms. The concept of hydrogen probes is to detect the amount of hydrogen permeating through the steel by mechanical or electrochemical measurement and to use this as a qualitative indication of corrosion rate.
Overall, monitoring techniques have proven to be successful in reducing facility shutdown time, extending the life of the asset, and saving companies significant costs. It is not uncommon to apply multiple techniques at the same time.
(vi)Sand / Erosion Monitoring These are devices which are designed to measure erosion in a flowing system. They find wide application in oil/gas production systems where particulate matter is present.
- When is Corrosion Monitoring Performed?
Corrosion monitoring plays a vital role throughout the equipment lifecycle. Inspection and
monitoring strategies and techniques may change according to the age and condition of equipment.
Therefore, inspection and monitoring strategies should be reviewed at specific intervals at the
owner-operator’s discretion.
- Where is Corrosion Monitoring Performed?
Corrosion remains one of the biggest threats to the petroleum industry. Therefore, corrosion
prevention is a primary concern especially in equipment such as flowlines, transportation pipelines,
vessels, water systems, boilers, vacuum towers, cooling systems, amine systems, and crude oil
systems. These systems are typically the most susceptible to producing corrosive environments.
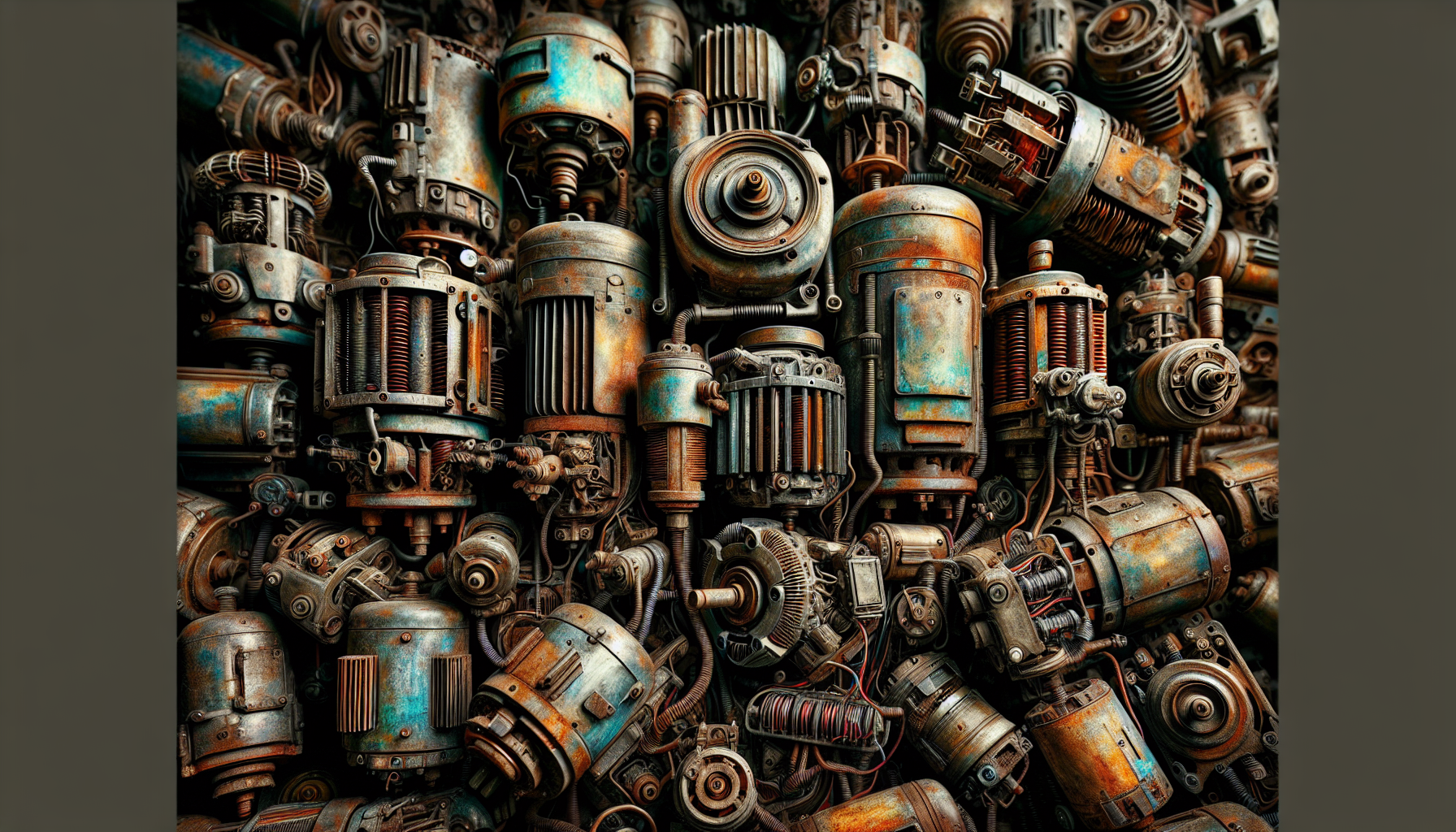
Generated image of rusted corroded motors